<4> ‘불량 제로 도전’ 품질 완결 시스템
개발 3년 만인 2014년 국내 첫 도입수작업 대신한 IT, 결함 땐 즉각 통보
아이오닉 생산 31라인 공정당 64초
올해는 품질 테스트 통과율 92% 목표
스마트공장 4단계 중 ‘고도화’만 남아
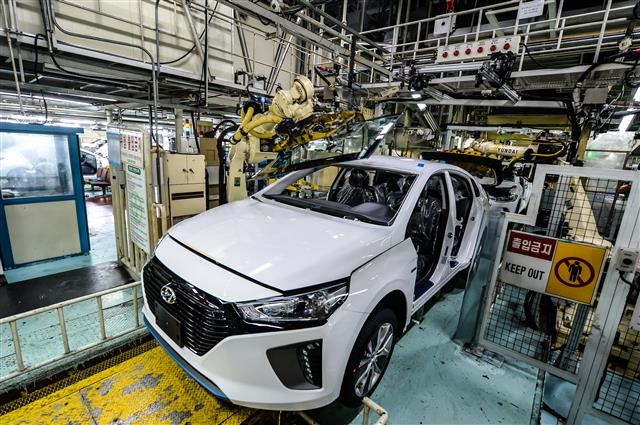
현대자동차 제공
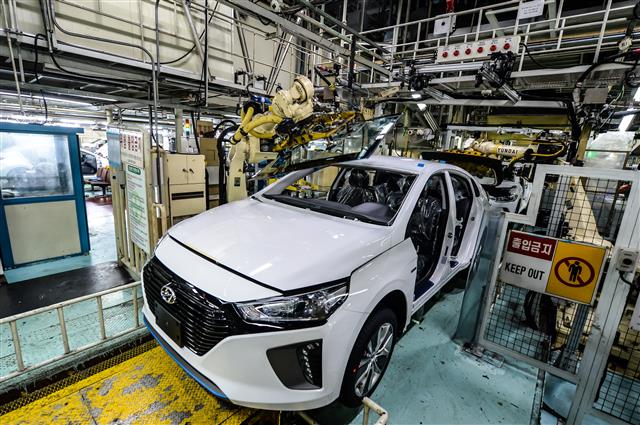
현대차 울산3공장에서 로봇이 아이오닉 하이브리드의 앞유리를 장착하고 있다.
현대자동차 제공
현대자동차 제공
지난 12일 오후 현대차 울산3공장. 품질 테스트에서 결함이 발견되자 곧바로 모니터에 결함 사유가 떴다. 해당 공정에도 즉시 통보가 됐다. 차량은 수정 작업장으로 옮겨졌다. 기존에 수작업으로 진행되는 일들이 정보기술(IT)과 접목되면서 보다 효율적으로 바뀐 것이다. 불량률 ‘제로’에도 도전할 수 있게 됐다. 과거에는 사람이 직접 종이에 결함 내용을 써서 다음 공정에 전달했기 때문에 전달 과정에서 종이가 사라지면 결함이 수정되지 않은 채 출고될 수도 있었지만, 이제는 전자펜으로 결함 유무를 체크하기 때문에 수정 작업이 완료되지 않으면 출고 자체가 안 된다.
실시간으로 결함이 보고되면서 모니터에 뜨는 ‘직행률’(불량 없이 한 번에 통과한 비율) 수치도 계속 바뀌었다. 오후 1시 현재 ‘직행률’은 89.23%. 100대 중 약 89대만 수정 작업 없이 무사 통과했다는 의미다. 조립, 검차 주행, 수밀(물이 새는지 점검하는 검사) 등 세 가지 품질 테스트에서 ‘트리플 100점’을 받지 못하면 결함 차량으로 분류된다. 1월 1일부터 11일까지 누적 직행률은 87.2%로 내부적으로 정한 목표치는 달성했다. 올해 12월 92.2%까지 올리는 게 목표다.
1990년 완공 이후 ‘아반떼’ 생산기지로 이름을 날린 울산3공장은 2014년 현대차 국내 공장 중 처음으로 ‘품질 완결 시스템’을 도입했다. 당시 품질관리부장이었던 송근수 생산3실장(이사)은 “개발에만 3년이 걸렸다”면서 “문제점을 실시간으로 공유할 뿐 아니라 데이터를 분석하는 작업도 가능해졌다”고 말했다. 이 시스템은 신차를 생산할 때 초기에 반복되는 결함을 잡아 낼 수 있다는 장점이 있다. 아반떼와 함께 친환경차인 아이오닉을 생산하는 3공장 31라인은 공정 하나당 소요 시간이 64초에 불과하다. 옆 라인인 32라인(100초)보다 훨씬 짧다. 아이오닉 하이브리드, 아이오닉 전기차(EV)에 이어 곧 아이오닉 플러그인 하이브리드(PHEV)도 양산할 예정이다. 다만 공정이 복잡하면 결함이 잦을 수밖에 없다. 현재 아이오닉 하루 생산량은 210여대. 전체 생산량 1400대 중 15%를 차지하고 있지만 미국, 유럽 등 해외 시장에서 주문이 밀려들면서 생산이 늘어나는 추세다. 송 실장은 “속(부품)을 채워 넣는 의장 공정에서는 사람의 손이 닿다 보니 실수가 발생한다”면서 “올해부터 안정화 단계에 접어들면 불량률은 현격하게 줄어들 것”이라고 말했다.


울산3공장에서 효과를 본 품질 완결 시스템은 아산공장에 이어 울산 2, 4공장까지 확대 적용됐다. 울산 1, 5공장도 도입 중에 있다. 울산공장은 생산성 지표 중 하나인 HPV(차 한 대를 만드는 데 걸리는 시간)가 약 29시간으로 아산공장(18시간), 해외 공장 평균(16~17시간)에 비해 나쁘지만 스마트화로 극복할 계획이다. 울산공장에는 진동·전류 센서를 주요 설비에 부착해 이상 징후를 사전에 감지하는 설비 예방진단 시스템, 지능형 용접기, 각종 자동검사 시스템, 품질생산성 모니터링 시스템 등이 구축돼 있다. 향후 투자 효과 등이 증명되면 클라우드, 빅데이터, 사물인터넷(IoT), 가상물리시스템(CPS) 기술도 점차 적용한다는 방침이다.
아산공장은 지난해 도장 공정에 국내 최초로 로봇 카메라를 설치했다. 페인트 외관 이물질 검사를 위해서다. 사람의 눈에 보이지 않는 이물질도 검수 단계가 아닌 도장 공정에서 잡아내면 비용을 최소화할 수 있다. 스마트워치도 개발했다. 자주 쓰이지 않는 부품(비선호 사양 또는 지역 옵션)을 탑재할 경우 모니터에 사양 정보가 뜨고 알람도 울리지만, 작업자가 인지하지 못하면 실수로 다른 부품이 들어갈 수 있기 때문에 이를 방지하기 위해 손목에 시계 형태의 ‘개인 모니터’를 만들어 준 것이다. 아직 울산공장에는 도입하지 않았다.
스마트 공장은 사물인터넷, 가상물리 시스템을 기반으로 제조의 모든 단계가 자동화되고, 가치사슬 전체가 하나의 공장처럼 실시간 연동되는 생산 체계를 의미한다. IT 활용 정도에 따라 크게 기초, 중간1, 중간2, 고도화 등 4단계로 나뉜다. 고도화는 설비, 시스템이 자체 판단에 따라 자율 생산하는 체제로 아직 국내 공장 중에는 단 한 곳도 없다. 현대차도 자체 진단에서 중간 2단계(실시간 공장 자동 제어)에 속해 있다고 봤다.
●스마트공장 3단계 이른 중소·중견기업 2.6% 뿐
스마트 공장으로 전환한 중소·중견기업 2611개(2016년 9월 말 기준) 중 중간 2단계는 2.6%에 불과하다. 대부분 기초(81.2%) 또는 중간1(16.2%) 수준에 머물러 있다. 상황이 이렇다 보니 현대차는 삼성, LG 등과 함께 중소 협력사 스마트 공장 보급 사업에도 나섰다. 반월시화산업단지에 입주한 중소협력사 100여곳과 광주 지역 중소기업 200곳을 우선 지원한다.
울산 김헌주 기자 dream@seoul.co.kr
2017-01-16 6면
Copyright ⓒ 서울신문. All rights reserved. 무단 전재-재배포, AI 학습 및 활용 금지