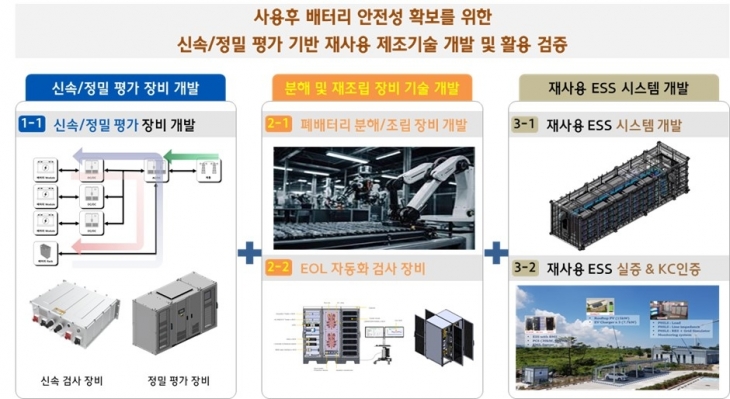
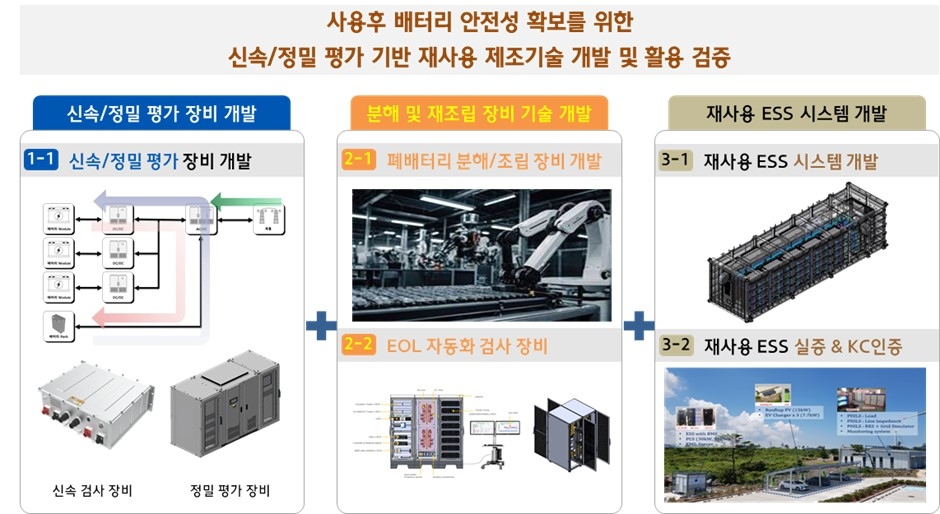
소재부품기술개발(협력모델) 과제 개발 내용. <사진=덕양산업, 인텍FA,(유)레드,한국섬유기계융합연구원(KOTIMI)>
산업통상자원부에서 지원하고 한국산업기술기획평가원(KEIT)에서 주관하는 해당 사업은 총사업비 230억원(정부출연금 180억원 지원)이 투입되어 ‘사용 후 배터리 안전성 확보를 위한 신속/정밀 평가 기반 재사용 제조 기술 개발 및 활용 검증’을 진행할 예정이다.
자동차 산업계는 최근 전기차의 보급 확대에 따른 사용 후 배터리의 무분별한 처리 문제가 또 다른 환경 오염과 막대한 자원 낭비의 이슈로 대두되고 있다. 이러한 문제를 해결하기 위해 지난 7월 기획재정부에서는 ‘사용 후 배터리 산업 육성을 위한 법·제도·인프라 구축 방안’을 발표했다. 이번 방안은 사용 후 배터리 산업을 육성하고, 글로벌 통상 규제에 선제적으로 대응할 수 있도록 관리 체계를 고도화하는 것에 초점을 두고 마련되었다.
이러한 정책 변화와 문제를 해결하기 위해 덕양산업은 소재부품기술개발(협력모델) 국책과제를 통해, 사용 후 배터리 사업에 필요한 진단, 분해, 재조립 장비 등 인프라를 구축하고 재사용 ESS 시스템 개발과 실증 및 인증을 통해 양산성과 경제성을 동시에 확보하고자 한다.
이미 회사는 다년간의 배터리 모듈, 배터리팩 관련 기술 개발과 생산을 통해 최근에는 열전이 방지 구조, 고효율 열관리 배터리팩 시스템, 대형(1MWh급 이상) 선박용 ESS 시스템을 개발하며 화재 안전 기술 개발을 비롯한 다양한 연구 경험을 가지고 있다. 이러한 축적된 기술을 적용하여 사용 후 배터리 모듈 단위로 구성된 재사용 ESS 시스템(30KWh, 300KWh, 1MWh)을 개발할 예정이다.
한편, 덕양산업은 재사용 사업에 대한 양산 체계 구축 및 제품 안전성 확보를 위해 사용 후 배터리 진단 장비, 분해·재조립 장비, EOL 성능 평가 장비 업체와 실증 및 인증 평가 기관 등으로 컨소시엄을 구성해 이번 과제를 진행한다.
폐자동차 자원순환센터를 운영하는 기업으로부터 사용 후 배터리팩을 공급받아 30분 이내에 배터리팩의 상태를 신속히 진단할 수 있는 정밀 평가 장비를 개발하여 사용 가능한 배터리팩을 선별한다. 선별된 배터리팩을 모듈 단위로 분해하기 위한 분해 장비, 이를 잔존가치 등급별로 구성하여 조립할 수 있는 재조립 설비도 구축한다.
또한 폐배터리 입고부터 재조립된 제품이 재사용 되기까지 모든 데이터를 관리하기 위해 전 주기 이력 관리 시스템을 구축한다. 이렇게 제작된 재사용 제품에 대한 사용성 및 안전성 확보를 위해 계통 안정화용, 신재생에너지 연계형, 자가소비형 ESS 실증 평가를 실시하고 KC 10031 인증 (사용 후 전지의 재사용을 위한 리튬 이차전지의 안전 요구사항)을 획득하여 안전성을 확보할 계획이다.
덕양산업 정홍규 사장은 “ESS 설계 기술과 양산 체계 구축을 통한 덕양산업의 재사용 ESS 시스템은 태양광이나 풍력 발전과 같은 친환경 에너지의 전력용 ESS와 상업용, 통신용으로 판매되고 더 나아가 가정용 ESS 시장 성장에 맞춰 확대될 것으로 보인다”며, “이에 따른 재사용 ESS사업 매출액은 설비 1대당 100MWh 생산 기준으로 2030년 약 900억원에서 2040년 약 2,700억원으로 증가할 것으로 예상되며, ESG 및 탄소 중립 사회 실현에도 기여하여 재사용 사업에서 선도적인 역할을 할 것으로 기대된다”고 밝혔다.